How Printing Ink Dries
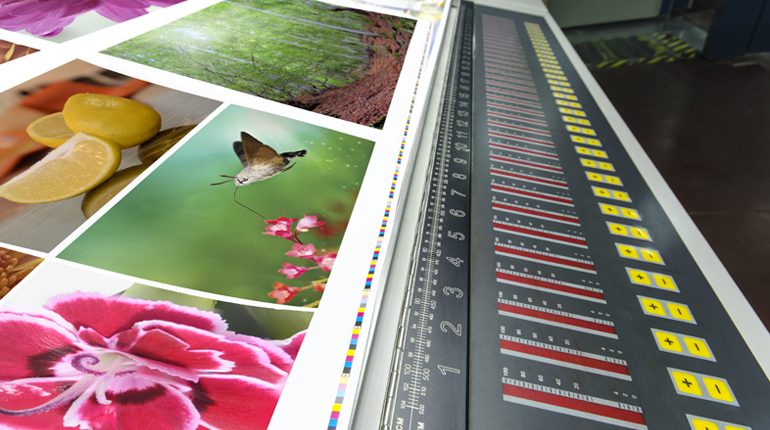
Ink chemists have invented numerous ways to make ink dry, but litho and letterpress inks dry primarily by two methods; absorption and oxidation.
Absorption means that the ink soaks into the stock like water into a sponge. Oxidation means that the varnishes in the printed film will harden by chemical process when exposed to air and form a solid layer, which binds the pigment to the printed surface.
Offset inks use both methods of drying, but dry predominantly by one method or the other. Van Son Rubber Base Plus inks dry 100% by absorption, making it suitable for all uncoated stocks.
Van Son Quickson offset offset inks dry 50% by absorption and 50% by oxidation. It can be used on coated and uncoated stocks. Van Son Tough Tex offset inks dry 100% by oxidation. Non-porous surfaces, such as foil and plastics require this type of ink.
Factors that affect process ink drying
Fountain water acidity
As the process ink and fountain solution come together on the rollers of a lithographic press, the ink will pick up 10%to 30% water in the form of tiny droplets within the body of the ink. This is normal and the water will dissipate in the print. If the pH of the fountain solution is too acidic, the ink/water balance is upset and three things can happen that will affect drying.
Firstly, the acid can attack the driers in the ink, rendering them inactive and slowing up the oxidation process. On coated paper, this slow drying can cause the varnish to drain into the paper coating instead of setting on the surface and binding the pigment to the paper. This results in a chalky ink surface that can only be corrected with overprint varnish.
When printing with Tough Tex on non-porous stock, such as plastic or foil, excessive acidity can cause severely slow drying because the water is not absorbed by the stock, but rather stays with the ink and actually becomes more concentrated in acid as it slowly evaporates.
Secondly, excessive acid can break down the water resistance of an ink, requiring the use of more water to prevent scumming. The ink takes on more water, resulting in mottled print as the water globules become larger within the printed film.
Thirdly, excessive acid can sensitise your metal rollers causing them to strip, i.e., accept ink unevenly.
Humidity
Relative humidity can cause paper to become damp and limp. Ink takes a long time to dry on paper in this condition. The effect of moisture on drying is the same, whether it comes from paper, the atmosphere or the press fountain.
This situation can be corrected by winding the printed sheet or by placing the stock on edge and blowing dry, heated air between the sheets.
Temperature
Ink dries faster on warm stock than on cold. The drying time is reduced about 25% for each 6°C. increase in temperature. This is true for inks that dry by absorption or oxidation. Heat lowers the viscosity of absorbing inks so they strike into the stock more rapidly. Heat accelerates the chemical reaction of inks that dry by oxidation.
Ink coverage
Occasionally, a small printed area will take longer to dry than a large one. With each impression, the form rollers travel across the plate, which is mostly covered in water, except the small image area.
The form rollers pick up this water and feed it back into the ink distribution system. The ink may get tired of this continual barrage of water and start to emulsify. In contrast, a large coverage requires faster ink takeoff by the form rollers and a more rapid flow of ink from fountain to blanket with much less exposure to water.
Increasing the level of isopropyl alcohol will reduce the amount of water needed to keep the plate clean.
In conclusion
When the failure of ink to dry is discovered, the damage has already been done, and at best, the result is an inconvenient delay in finishing the job. Sometimes, delay involves serious loss and it is necessary to apply a remedy to complete the job on time. Remedies are inconvenient and often expensive. Intelligent planning avoids drying problems. By familiarising yourself with possible ink drying problems, you should be able to avoid them.
Need any other litho print supplies?
We supply a full range of Print Consumables, including Standard Pantone Ink, Pantone Matching Guides, Litho Print Chemistry, Litho Printing Blankets and OverPrint Varnishes.
- Clive Harper