Water Based Coating Trouble Shooting Guide
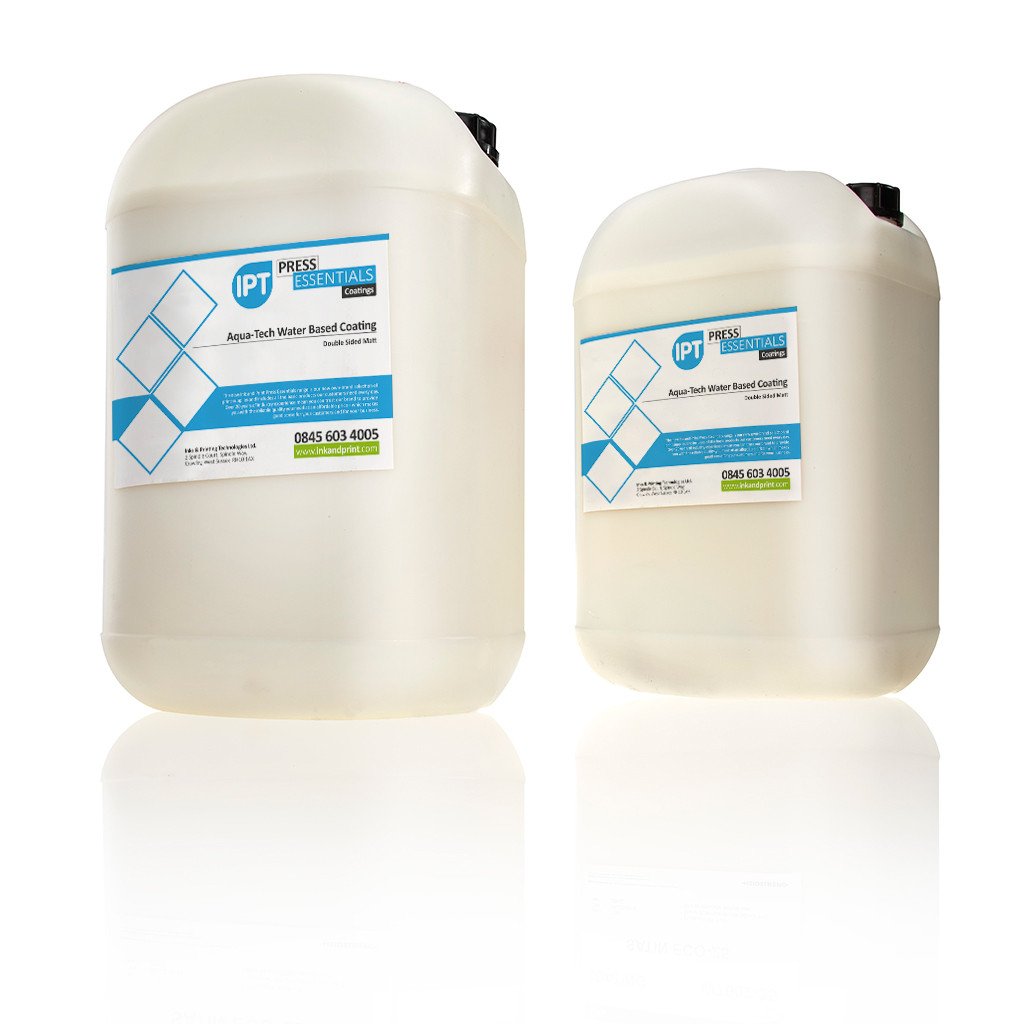
Ink & Printing Technologies
Water Based Coatings Trouble Shooting Guide.
Wetting: - Poor wetting can be the result of the following factors: -
- Pressure between blanket and impression cylinders
- High ink film weight
Excessive pressure between blanket and impression cylinder of the coating unit may result in inadequate wetting of the blanket cylinder, leading to a build-up of ink on this cylinder. This results in patches on the coated sheet where the ink build up is restricting the coverage. The obvious remedy in such cases is to reduce pressures to the bare minimum.
Heavy film weights of oil-based inks may lead to unacceptable wetting of the water-based emulsion. If heavy film weights are anticipated an intense ink system should be considered.
Curl :-Substrate curl is heat related, and is caused by the evaporation of moisture from the board. Some low grammage stocks (i.e., under 80gsm) can also be affected by the evaporation of volatiles in the drying process of water-based coatings. In the case of substrate curl on stocks above 80gsm, it can be beneficial to reduce I.R lamps, air knives etc. to the bare minimum monitoring closely for blocking. This reduction in heat allows a much slower release of moisture from the board, promoting lower curl.
Substrates under 80gsm may require a specialist low curl formulation. Please contact IPT for advice.
Crazing
Crazing, also known as the ‘egg-shell’ effect, is the result of a coating drying too fast often over heavy ink coverages, therefore creating a cracked appearance. Crazing can be reduced with the addition of a retarder or by use of a specialist coating.
Gloss
Problems concerning gloss are generally rare and are often related to unrealistic views on the kind of gloss levels which can be achieved. Requests are often made for levels like that of UV, however it is important to note that whereas UV has a solids level of 100%, water-based averages at around 45% solids. This means that 55% of the original water base body is lost to the atmosphere, therefore making comparative matches to UV very unlikely. Coatings that do exhibit high gloss (Single Sided Emulsions offer higher gloss levels) are generally slow drying giving reflection readings of between 70 and 80% dependent on the stock used. Gloss can be increased by slowing the speed of the press, using a larger Anilox or by increasing the sweep. If the decision is made to increase film weight, work should be monitored for blocking.
Viscosity
Viscosity’s are generally dictated by the type of coating unit and the level at which the printer feels happy to run. Most water-based coatings applied via a dedicated coating unit will have a viscosity of between 30- and 60-seconds DIN 4 @ 25°c. Modifications to reduce viscosity can be made using water.
Rub
Rub problems are rare but are usually caused by heavy ink coverage’s or by substrates where drying is inhibited. If heavy ink coverage is anticipated, it may be beneficial to use an intense ink series to keep the film weight low. Substrates such as foils, polyethylene papers and recycled stocks may require a special coating to give optimum protection.
Foaming
Water based coatings are designed to minimize the formation of foam, however on large presses where diaphragm pumps are used to circulate coatings (sometimes from containers as large as 200kg) the generation of foam can become a problem. In severe cases the formation of foam can create increases in viscosity and the problems associated with viscosity appear.
Slip
Slip is an important factor in the carton printing industry and depending on the packaging line requirements low slip or high slip may be required. Slip is controlled by a blend of waxes and silicones and can be specified by using slip angles or static and dynamic measurements. Film weights and ink coverage can dictate slip, with low coverage work generally giving higher slip results (i.e., more slippery) than work with heavy coverage.
Blocking
Blocking or ‘set-off’ can be initiated by several factors including: -
- Extremes of Heat
- Insufficient Spray Powder
- Incorrect Coating
- Film-weight too high
Stack temperatures should not fall below 27 or Above 36 ºC. Cold stacks mean that insufficient heat was applied as the sheet passed through the swan neck, thus resulting in slow drying. Hot stacks will keep the coating soft, increasing the possibility of re-wetting and therefore blocking.
Heavy boards, rapid press speeds, very high gloss coatings and immediate back-ups all require extra spray powder. A medium particle size is usually sufficient with a medium to high spray coverage.
Work to be backed up and coated on the second side will require a double-sided Coating. Regular, single sided emulsions, usually High Gloss, will re-wet when backed up resulting in serious blocking.
Double sided emulsions are generally faster drying and consequently slightly lower in Gloss.
For any further technical assistance or advice regarding Water Based Coatings, please contact us:
Tele: 01293 531926
Email: tech-assist@inkandprint.com
- Clive Harper